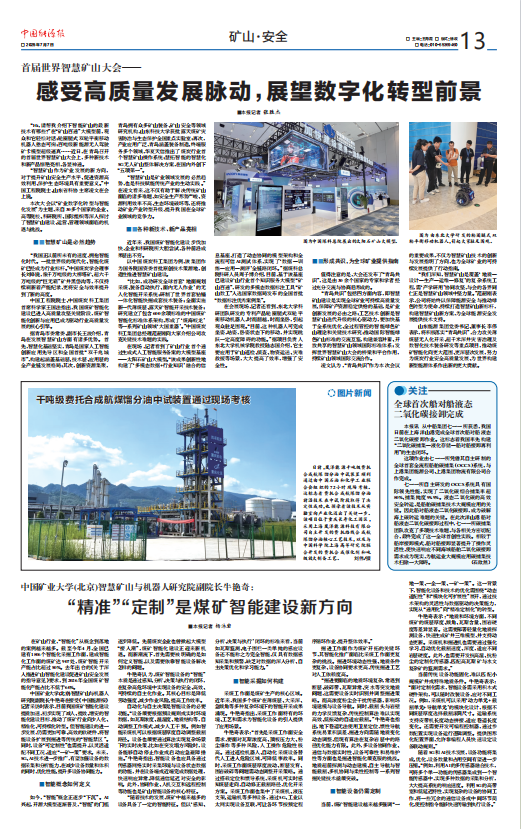
在矿山行业,“智能化”从概念到落地的案例越来越多。截至今年4月,全国已建有1806个智能化采掘工作面,建成智能化工作面的煤矿达907处,煤矿智能开采产能占比超过50%。去年出台的《关于深入推进矿山智能化建设促进矿山安全发展的指导意见》要求,到2026年全国煤矿智能化产能占比不低于60%。
中国矿业大学(北京)智慧矿山与机器人研究院副院长牛艳奇在接受《中国能源报》记者采访时表示,目前我国煤矿智能化建设提质加速,初步实现了减人、提效、增安的智能化建设目标,推动了煤矿行业向少人化、精准化、可持续化转型。但智能建设的进一步发展,仍需更加可靠、高效的软硬件,将智能设备扩展到掘进等传统的“智能禁区”。同时,设备“可定制性”也需提升,以灵活适配不同工况,适应“一矿一策”要求。未来,5G、AI技术进一步推广,有望加强设备的数据采集和分析能力,在减少设备数量和体积的同时,优化性能、提升多设备协同能力。
■智能概念如何定义
如今,“智能”概念正逐步“下沉”。AI兴起,开源大模型逐渐普及,“智能”的门槛逐步降低。先前煤炭企业也曾掀起大模型“接入潮”,煤矿智能化建设正迎来新机遇。而新潮流下,首先需要被明确的是如何定义智能,以及需要依靠智能设备解决怎样的问题。
牛艳奇认为,煤矿智能设备的“智能”本质是通过感知、分析、决策与执行的闭环,在复杂高危环境中实现设备的安全、高效、可持续的自主化作业。其核心目标是降低劳动强度、减少作业风险、提高工作效率。
自动化与自主决策是智能设备的必要功能。“设备须要根据预设规则或实时环境数据,如瓦斯浓度、温湿度、地质结构等,自动调整工作模式,减少人工干预。例如智能采煤机可以根据煤层厚度自动调整截割路径。设备也须要通过算法实现复杂场景下的实时决策,比如在突发塌方风险时,设备能够自动停止作业或启动应急避障措施。”牛艳奇指出,智能设备也应具备通过传感器网络实时采集环境与设备状态数据的功能,并在设备端或近端完成数据处理,快速响应异常,降低通信延迟对安全的影响。此外,协同作业、人机交互和远程控制等功能也是矿山智能设备的核心特征。
“随着技术的发展,煤矿中越来越多的设备具备了一定的智能特征。但以‘感知、分析、决策与执行’闭环的标准来看,当前如瓦斯监测、电子围栏一类单纯的感应设备还不能称之为完全智能,仅具有数据感知采集和预警,缺乏对数据的深入分析、自主决策优化和学习能力。”
■智能采掘如何构建
采煤工作面是煤矿生产的核心区域。近年来,我国多个煤矿在薄煤层、大采深、急倾角等多种复杂环境下的智能开采成果涌现。牛艳奇指出,采煤工作面特有的环境、工艺和需求为智能化设备的引入提供了应用场景。
牛艳奇表示:“首先是采煤工作面安全需求,要面对瓦斯浓度高、顶板压力大、粉尘爆炸等多种风险,人工操作危险性极高。通过巡检机器人、自动化采煤设备替代人工进入危险区域,可降低事故率。同时,采煤工作面煤层厚度波动、断层发育、围岩破碎等问题需动态调整开采策略。通过搭载定位和惯导系统,采煤机可实时感知煤层走向,自动修正截割路径,优化开采方案。采煤工作面也集中了采煤机、液压支架、运输机等多种设备,通过5G、工业以太网实现设备互联,可让各环节按预定程序循环作业,提升整体效率。”
掘进工作面作为煤矿开拓的关键环节,其智能化推广面临比采煤工作面更复杂的挑战。掘进环境动态性强、地质条件更复杂、设备协同要求更高,传统掘进工艺对人工依赖度高。
“掘进要面临的地质环境复杂,常遇到断层、破碎带、瓦斯异常、突水等突发地质问题,这需要设备实时识别并调整掘进策略。而高浓度粉尘会干扰传感器,影响环境建模与设备导航。同时,截割头与岩壁的力学反馈复杂,传统控制算法难以实现高效、低振动的自适应截割。”牛艳奇也指出,地下巷道无法使用卫星定位,惯性导航系统易累积误差,掘进方向需随地质变化动态调整,但现有算法在复杂岩层中的路径优化能力有限。此外,多设备协同作业、通信与数据实时性、设备可靠性和易维护性等方面也是掘进智能化须克服的挑战。地质超前探测与动态建模、自主导航与智能截割、多机协同与柔性控制等一系列智掘关键技术亟须突破。
■智能设备仍需定制
当前,煤矿智能建设越来越多强调“一地一策、一企一策、一矿一策”。这一背景下,智能化设备和技术的优化需围绕“动态适配性”和“模块化可扩展性”展开,通过技术架构的灵活性与数据驱动的决策能力,实现从“通用化”向“精准定制化”的转型。
牛艳奇表示:“地质和环境方面,不同煤矿的煤层厚度、倾角、瓦斯含量、围岩硬度等差异显著。这需要部署轻量化地质探测设备,快速生成矿井三维模型,并支持动态更新。采煤机和掘进机也需要通过强化学习,自动优化截割速度、深度,适应不同岩层硬度。此外,也需要开发抗高湿、抗粉尘的定制化传感器,匹配高瓦斯矿与水文复杂矿的监测需求。”
当前传统设备功能固化,难以匹配小规模矿井或特殊地质条件。牛艳奇表示:“面对定制化需求,智能设备需采用积木式硬件架构,可以随时改装设备,应对不同工况。例如,采煤机可以采用‘动力单元+截割单元+导航单元’的模块化设计,根据不同煤层厚度选择截割滚筒尺寸。运输系统支持皮带机长度动态拼接,适应巷道长度变化。还需要开发可编程控制器,通过参数配置实现设备运行逻辑调整。提供图形化配置界面,允许非编程人员快速设定设备联动规则。”
随着5G和AI技术发展,设备功能将集成、优化,设备数量和占用空间有望进一步压缩。“例如,利用AI的多传感器融合技术,可将多个单一功能的传感器集成到一个智能传感器中,实现多种数据的采集和分析,大大提高系统的响应速度。利用5G的高带宽和低延迟特性,实现复杂的设备的协同工作,将一些冗余的通信设备或中间环节简化,使控制指令能够快速传输到执行设备。”